Sign up for our Green Box newsletter for more information, helpful tips or exciting product news. Get an additional €5 discount¹ on your next order.
¹Redeemable from a purchase value of €50 and only once as a newsletter subscriber:in. All data will be treated confidentially. Unsubscription is possible at any time
- ✔ Exclusive offers for subscribers
- ✔ Exciting news
- ✔ Helpful tips
- ✔ New products
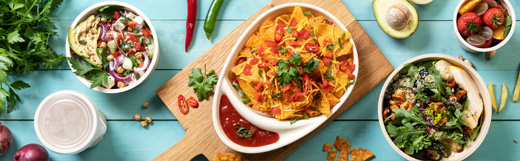
Would you like to read more such articles, or do you have a critical comment on the content? Then please send us an email with a reference to the specific article to feedback@greenbox.bio. This way we can continue to provide you with interesting content.